Getting My Alcast Company To Work
Getting My Alcast Company To Work
Blog Article
See This Report on Alcast Company
Table of ContentsThe smart Trick of Alcast Company That Nobody is DiscussingSome Known Facts About Alcast Company.The 20-Second Trick For Alcast Company10 Simple Techniques For Alcast CompanyThe 10-Minute Rule for Alcast CompanyThe Greatest Guide To Alcast CompanyExcitement About Alcast Company

If you assume that a functioned alloy might be the most effective for your task, have a look at some of our articles that explain more about certain functioned alloys, such as Alloy 6061 and Alloy 6063. On the other hand, if you think a cast alloy would certainly be much better for you, you can learn much more regarding some actors alloys in our Alloy 380 and Alloy 383 write-ups (coming quickly).
The Best Strategy To Use For Alcast Company
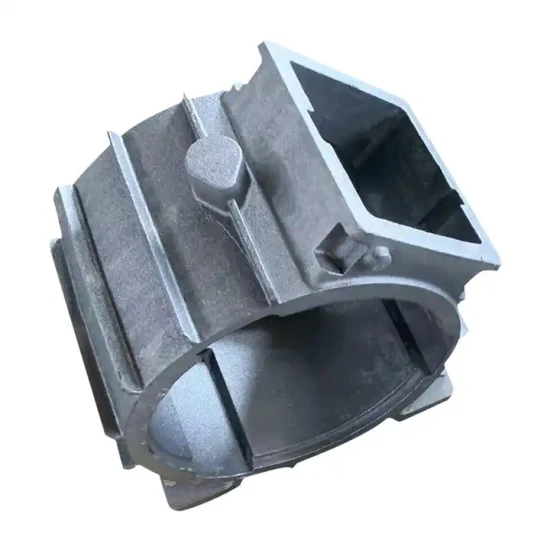
Having the experience and sector expertise to craft your castings for optimal production and high quality results will enhance the task. Making light weight aluminum spreading calls for a facility collection of procedures to achieve the right results. When picking a new aluminum foundry to partner with, ensure they have comprehensive industry experience and are well-informed regarding all elements of the aluminum casting process: layout, manufacturing, product evaluation, and product testing.
(https://www.metooo.io/u/a1castcmpny)The foundry must also have a tried and tested record of delivering exceptional items that meet or surpass customer assumptions. Quality control must also go to the top of your listing when choosing a light weight aluminum foundry. By collaborating with a qualified factory that complies with the criteria for high quality control, you can shield the stability of your item and ensure it satisfies your requirements.
The 6-Second Trick For Alcast Company
By choosing a business who offers solutions that fulfill or exceed your product needs, you can be certain that your job will be completed with the utmost accuracy and effectiveness. Different components call for different production strategies to cast light weight aluminum, such as sand casting or die spreading.
Die casting is the name offered to the process of creating complex steel elements via use molds of the part, likewise called passes away. The procedure uses non-ferrous steels which do not consist of iron, such as aluminum, zinc and magnesium, as a result of the preferable residential properties of the metals such as reduced weight, higher conductivity, non-magnetic conductivity and resistance to corrosion.
Unknown Facts About Alcast Company
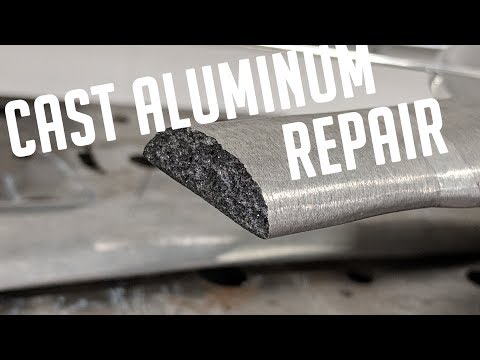
Regardless of the sub-process, the die spreading process can be damaged down right into 6 steps. After the purity of the alloy is examined, passes away are developed. To prepare the dies for casting, it is important that the dies are tidy, to make sure that no deposit from previous manufacturings continue to be. After cleansing, the ejection lubrication is related to the die to guarantee a smooth release.
The pure steel, likewise called ingot, is included in the heater and maintained at the molten temperature level of the steel, which is after that moved to the shot chamber and infused into the die (Foundry). The stress is after that preserved as the steel strengthens. Once the metal solidifies, the cooling procedure begins
Alcast Company Fundamentals Explained
The thicker the try this out wall surface of the component, the longer the cooling time since of the amount of indoor metal that also needs to cool down. After the element is totally cooled down, the die cuts in half open and an ejection system pushes the part out. Following the ejection, the die is closed for the next shot cycle.
The flash is the extra product that is cast throughout the process. This have to be trimmed off using a trim device to leave just the main element. Deburring eliminates the smaller pieces, called burrs, after the trimming procedure. The element is polished, or burnished, to give it a smooth surface.
Fascination About Alcast Company
Today, top manufacturers use x-ray screening to see the whole interior of parts without cutting right into them. To get to the ended up product, there are 3 key alloys made use of as die casting material to select from: zinc, light weight aluminum and magnesium.
Zinc is one of the most pre-owned alloys for die casting because of its reduced price of resources. It's also among the stronger and steady steels. And also, it has exceptional electrical and thermal conductivity. Its corrosion resistance also allows the parts to be durable, and it is one of the more castable alloys as a result of its reduced melting point.
The 3-Minute Rule for Alcast Company
As discussed, this alloy is among the most typically utilized, yet produces will, at times, choose light weight aluminum over zinc as a result of light weight aluminum's manufacturing advantages. Aluminum is extremely cost-effective and among the extra flexible alloys. Light weight aluminum is made use of for a variety of various items and sectors anything from window frames to aerospace products.
Report this page